Alcast Company - Truths
Table of ContentsFacts About Alcast Company RevealedThe Greatest Guide To Alcast CompanyAlcast Company Things To Know Before You BuyEverything about Alcast CompanyThe smart Trick of Alcast Company That Nobody is DiscussingThe Alcast Company PDFs
The subtle difference lies in the chemical material. Chemical Comparison of Cast Aluminum Alloys Silicon promotes castability by decreasing the alloy's melting temperature level and improving fluidness during casting. It plays a critical role in permitting detailed mold and mildews to be loaded accurately. Additionally, silicon adds to the alloy's toughness and put on resistance, making it useful in applications where sturdiness is important, such as auto components and engine components.It also enhances the machinability of the alloy, making it easier to process right into completed products. In this method, iron adds to the overall workability of aluminum alloys. Copper enhances electrical conductivity, making it beneficial in electric applications. It additionally boosts deterioration resistance and includes to the alloy's general toughness.
Manganese adds to the strength of light weight aluminum alloys and enhances workability (aluminum foundry). It is commonly made use of in wrought light weight aluminum items like sheets, extrusions, and accounts. The visibility of manganese help in the alloy's formability and resistance to splitting during manufacture processes. Magnesium is a lightweight component that gives strength and influence resistance to aluminum alloys.
The 6-Minute Rule for Alcast Company
Zinc improves the castability of aluminum alloys and assists control the solidification process during casting. It boosts the alloy's stamina and firmness.
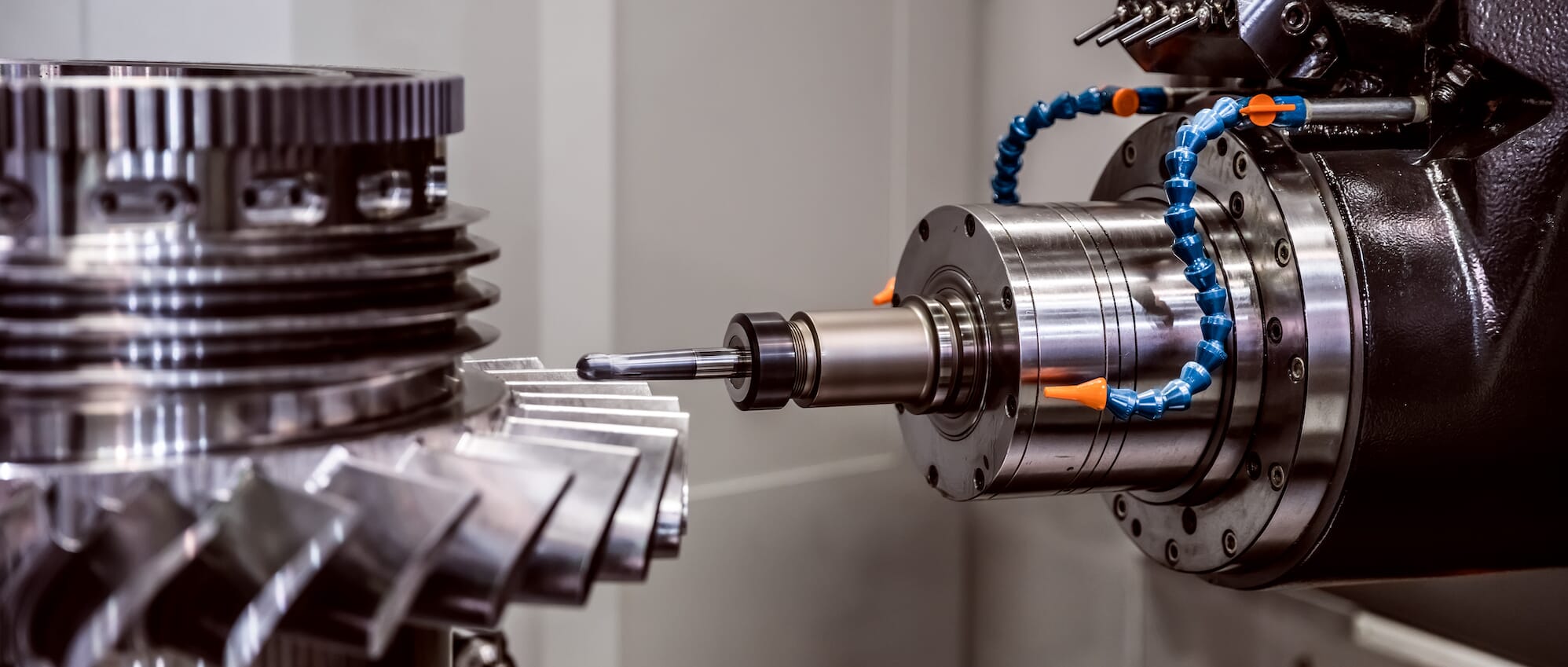
The primary thermal conductivity, tensile toughness, return strength, and elongation differ. Select appropriate basic materials according to the performance of the target product created. Amongst the above alloys, A356 has the greatest thermal conductivity, and A380 and ADC12 have the most affordable. The tensile limitation is the contrary. A360 has the finest yield toughness and the highest possible elongation rate.
The Ultimate Guide To Alcast Company
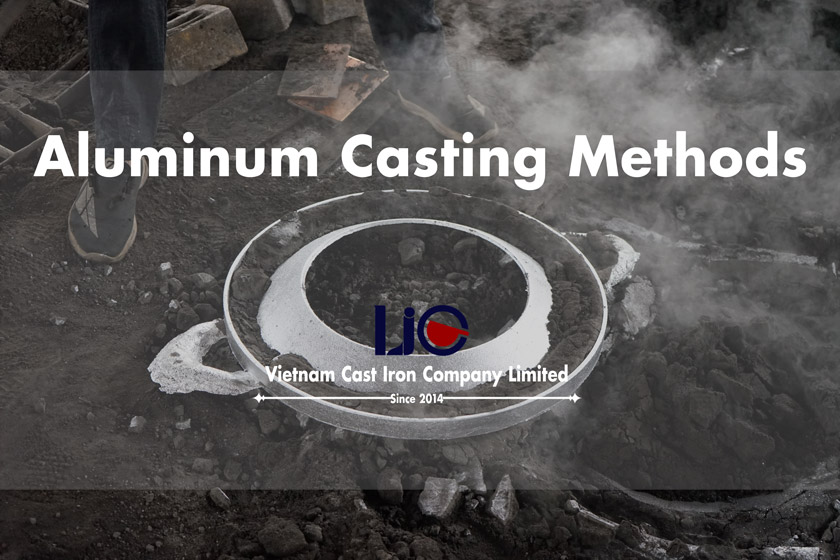
In accuracy spreading, 6063 is fit for applications where intricate geometries and premium surface coatings are paramount. Examples include telecommunication units, where the alloy's premium formability permits streamlined and aesthetically pleasing layouts while keeping architectural honesty. In a similar way, in the Lights Solutions market, precision-cast 6063 components produce classy and effective illumination fixtures that need intricate forms and excellent thermal efficiency.
The A360 exhibits remarkable elongation, making it excellent for facility and thin-walled components. In precision spreading applications, A360 is fit for sectors such as Consumer Electronics, Telecommunication, and Power Devices.
The Ultimate Guide To Alcast Company
Its one-of-a-kind buildings make A360 a valuable selection for precision casting in these sectors, improving product durability and quality. Aluminum alloy 380, or A380, is a commonly used spreading alloy with a number of distinctive features. It offers exceptional castability, making it an ideal selection for precision spreading. A380 exhibits good fluidness when molten, guaranteeing detailed and in-depth molds are accurately reproduced.
In precision casting, light weight aluminum 413 radiates in the Consumer Electronic Devices and Power Tools industries. This alloy's superior corrosion resistance makes it an excellent selection for outside applications, ensuring durable, sturdy items in the mentioned sectors.
See This Report about Alcast Company
When you have made a decision that the aluminum pass away casting procedure appropriates for your job, an essential next step is picking one of the most proper alloy. The aluminum alloy you select will substantially affect both the spreading procedure and the buildings of the end product. Due to this, you should make your choice very carefully and take an educated strategy.
Figuring out the most appropriate aluminum alloy for your application will mean weighing a broad selection of attributes. The first category addresses alloy qualities that impact the manufacturing process.
Not known Incorrect Statements About Alcast Company
The alloy you choose for die casting directly affects numerous facets of the casting procedure, like just how simple the alloy is to collaborate with and if it is prone to casting defects. Hot splitting, also known as solidification breaking, is a typical die casting problem for light weight aluminum alloys that can lead to interior or surface-level splits or splits.
Certain aluminum alloys are more susceptible to warm splitting than others, and your selection needs to consider this. One more typical issue found in the die spreading of aluminum is pass away soldering, which is when the cast sticks to the die walls and makes ejection hard. It can damage read this post here both the cast and the die, so you must look for alloys with high anti-soldering residential properties.
Rust resistance, which is currently a notable attribute of light weight aluminum, can differ considerably from alloy to alloy and is an essential characteristic to consider depending upon the ecological conditions your product will certainly be subjected to (aluminum metal casting). Use resistance is an additional home commonly looked for in light weight aluminum items and can distinguish some alloys